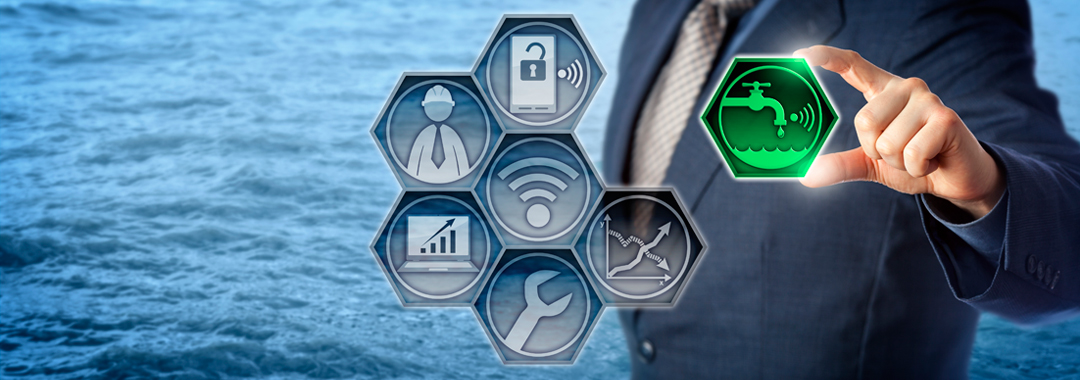
Proyectos:
Búsqueda de materias primas descarbonatadas
Dadas las elevadas emisiones de CO2 asociadas a la producción de clínker y cemento, el objetivo de este estudio ha sido llevar a cabo una búsqueda de materias primas, a ser posible descarbonatadas, en Aragón y alrededores que sirvan como sustituto parcial de la caliza y reducir así las emisiones de CO2 en la planta.
De las emisiones de CO2 que se producen en una planta de cemento, el 60% aproximadamente corresponde a la descarbonatación de la materia prima (caliza), asociadas estrechamente con la producción de clínker, el 40% restante proviene de los combustibles necesarios para realizar el proceso de clinkerización, donde sí se están introduciendo medidas de ahorro, incluyendo sustitución por otros combustibles alternativos, medida que ya se emplea desde el año 1992, usando hornos más eficientes energéticamente y optimizando los procesos de producción.
En cualquier caso, a pesar de que la caliza es indispensable para fabricar el clinker, sí se puede sustituir parcialmente por materiales alternativos que contengan calcio, reduciendo así las emisiones. Un elemento crucial es que dichas materias alternativas se encuentren cerca de la fábrica de cemento, aunque también tienen un papel importante la necesidad de acondicionamiento de dichas materias para su uso y para asegurarse de la estabilidad de su composición.< \p>
La simbiosis industrial, empleando recursos que carecen de utilidad en un sector y que se podrían usar en otro, y la búsqueda de materias primas descarbonatadas en las cercanías de las fábricas pueden así reducir considerablemente las emisiones de CO2. Existen subproductos generados por distintas empresas y residuos, con altos contenidos en calcio, sílice, alúmina y hierro que pueden ser empleados en el horno para tal fin.
De acuerdo con esto, se han identificado más de 70 empresas susceptibles de poseer residuos sustitutivos de la caliza en un radio de 200 km. En particular, la búsqueda se ha centrado en empresas que pudiesen generar los siguientes residuos:
- Estériles de minería, procedentes de explotaciones mineras
- Lodos procedentes de procesos industriales, entre ellos lodos procedentes de potabilizadoras, lodos procedentes del pulido y esmerilado de envases, lodos de neutralización de fluoruros
- Lodos de papeleras, residuos del proceso de la fabricación de pasta de celulosa
- Escorias negras y escorias blancas siderúrgicas, procedentes de la fabricación de acero en hornos
- Lodos férricos de altos hornos, residuos de la industria siderúrgica
- Cascarilla de laminación, óxidos de hierro procedentes de procesos de fusión
- Residuos de rocas industriales, ornamentales y derivados, residuos procedentes del aprovechamiento de rocas minerales, entre otros, material fino procedente de la obtención de mármol.
- Cenizas volantes
- Espumas de azucarera, residuo procedente de la fabricación de azúcar de remolacha
- Cenizas de pirita, residuo de la obtención de ácido sulfúrico
- Cenizas de incineradora
- Residuos de reciclado de aluminio
- Residuos de construcción y demolición Residuos con fosfatos
- Residuos cerámicos
- Arenas de fundición
- Cenizas procedentes de la incineración de biomasa
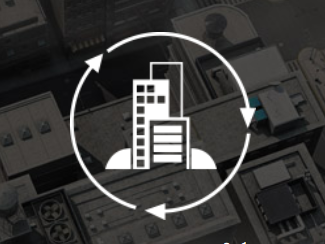
Análisis termoeconómico
El análisis termoeconómico de la planta de CEMEX de Morata de Aragón ha permitido diagnosticar en términos de costes exergéticos, la producción de clínker.
Mediante la termoeconomía podemos evaluar la cantidad y la calidad de las pérdidas de energía y materiales, además del coste de estas pérdidas en términos de recursos naturales. El cálculo de estos costes es semejante al análisis input-output, con la ventaja de que la unidad de cuantificación de todos los flujos es la exergía, con lo que los flujos son comparables por estar en la misma magnitud. Otra consecuencia del uso de la exergía es que introducimos el segundo principio de la termodinámica, por lo que la exergía de cada componente o instalación siempre disminuye.
El coste de un determinado bien puede definirse como la cantidad de recursos utilizados para producirlo, por lo tanto el coste exergético de un flujo de exergía es la exergía necesaria para producirlo. En este coste está incluida la exergía del flujo más las irreversibilidades de todos los procesos que han sido llevados a cabo para producirlo. Cuanto menos eficiente sea el proceso de producción del flujo, su coste aumenta. Además, no depende solamente del flujo, si no que depende de los flujos anteriores. En especial, depende de dónde hemos definido la frontera de nuestro sistema.
Así, para realizar el análisis termoeconómico, se obtuvo el diagrama de flujos, especificando todas las entradas y salidas de materiales y energía. A continuación se calculó la exergía de esos flujos. Finalmente se realizó el análisis termoeconómico del sistema, obteniendo los costes exergéticos unitarios de cada proceso. Aquéllos con mayores costes exergéticos unitarios fueron identificados como los procesos más ineficientes y donde mayor énfasis habría que realizar para optimizarlos.
Finalmente, partiendo del funcionamiento base de la planta, se plantearon posibles escenarios de mejora que pudiesen reducir los costes exergéticos: sustitución de materias primas por secundarias, cambio de equipos por otros más eficientes, aislamiento de equipos, etc, identificándose las que mayor impacto pudiesen tener.
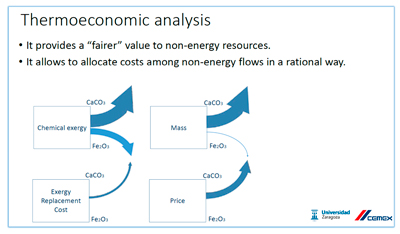
Estudio de dispersión de contaminantes
En el estudio de dispersión de contaminantes, se realizó un modelo a través del programa P.E.C.A. (Programa de Evaluación de la Calidad Ambiental) desarrollado en el Área de Mecánica de Fluidos de la Universidad de Zaragoza. Para dicho estudio fueron necesarios datos orográficos, meteorológicos, de emisiones y ubicación y características físicas de la chimenea. Consecuentemente, se obtuvieron isolíneas de inmisión de varios contaminantes: NOx, SOx, CO y partículas.
Con el modelo gaussiano de dispersión de contaminantes utilizado se pudieron así determinar los niveles máximos de inmisión de contaminantes en el entorno inmediato de la cementera y aquellas zonas en las que la concentración de contaminantes supera un determinado valor.
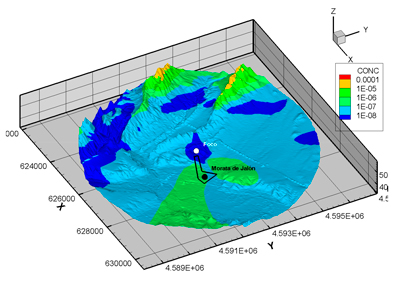
Economía circular en Utrillas
El 13 de Abril de 2016 se convoca una reunión en Utrillas para impulsar la economía circular en el entorno, dados los buenos mimbres existentes tanto a nivel industrial, como de recursos de la zona. Para ello se necesitan fundamentalmente tres ingredientes: voluntad empresarial (la más importante), apoyo institucional (para impulsarlo y para no incluir barreras legales) e investigación y desarrollo. En la reunión se pretende pues iniciar una colaboración interempresarial apoyada por instituciones locales e impulsada por una organización de investigación (CIRCE). A dicha reunión de trabajo asisten 17 personas pertenecientes a los tres ámbitos especificados arriba: el ayuntamiento de Utrillas; las empresas CEMEX, Casting Ros, Fertinagro, la consultora PF Energy y finalmente la Fundación CIRCE.
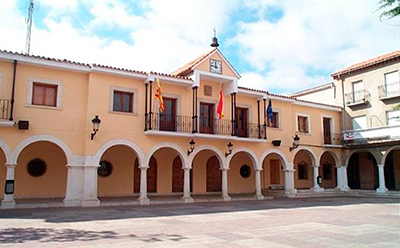